Look behind the glitz and glamour of global fashion, and you will find an ecologically harmful, anti-social industry largely unable to shed its capitalist dynamics. Its factories generate huge amounts of pollution and rely on underpaid, abused sweatshop labor. Fast fashion fills up landfills with mountains of cheap clothing discarded after a few uses. To keep consumption and sales going, fashion's relentless marketing machine peddles fantasies of luxury, rail-thin bodies, and sex appeal.
While this juggernaut may seem unstoppable, a brave and hardy band of creative insurgents is pioneering entirely new models of textile production, garment design, production and distribution. Their goals are to rehumanize and relocalize garment production, and to escape the hamster wheel of endless consumerism and economic growth.
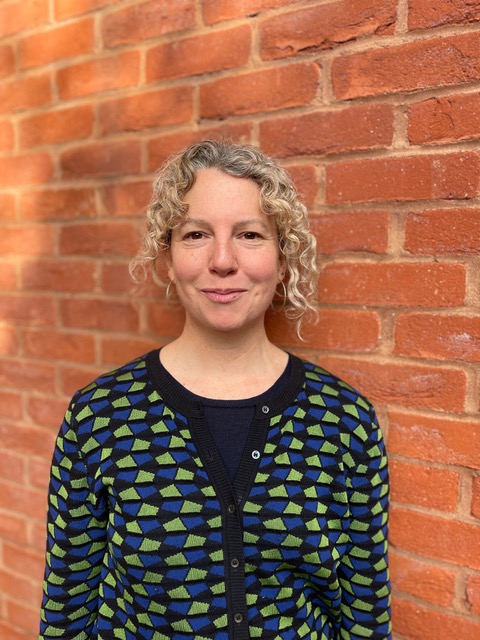
To get a better sense of what this grassroots global movement looks like, I recently spoke with British designer/ecologist/activist Zoe Gilbertson on my podcast, Frontiers of Commoning (Episode #56).
Gilbertson has worked in the fashion industry for more than 20 years -- for an athletic shoemaker in Germany, a major outdoor clothing brand in Canada, and eventually at her own startup company. But it slowly dawned on her that the ecological performance of major fashion houses was painfully modest if not an outright marketing deception.
Inspired by climate activists, coursework at Schumacher College in Devon, England, and by her father -- who helped start the fair trade movement -- Gilbertson decided to take a deeper plunge. With support from a Churchill Fellowship, she began an in-depth research project to explore the feasibility of bioregional fiber production. She wanted to figure out ambitious, practical ways of transforming fashion from the ground up (literally!).
Gilbertson toured dozens of innovative, little-known projects in Europe and the UK, focusing on the growing of bast fibers, chiefly hemp and flax (used in making linen). "I wanted to find out if we can find a balance between handmade and industrial extractive systems," Gilbertson said. "I wanted to look at the scale. Could we redevelop smaller-scale systems and make textiles much more localized and distributed, instead of creating huge infrastructures of factories and machinery to process and spin the fibers?"
More broadly, Gilbertson wanted to figure out how fiber-growing and textile production might be designed as an integrated bioregional system. Could local fiber agriculture be conjoined with local textile and garment production, and could bast fiber byproducts be used in food and building materials, and invigorate local culture? To search for answers, Gilbertson traveled throughout The Netherlands, France, Switzerland, Belgium, Spain, and Finland, and consulted with fibershed allies in Canada and the U.S.
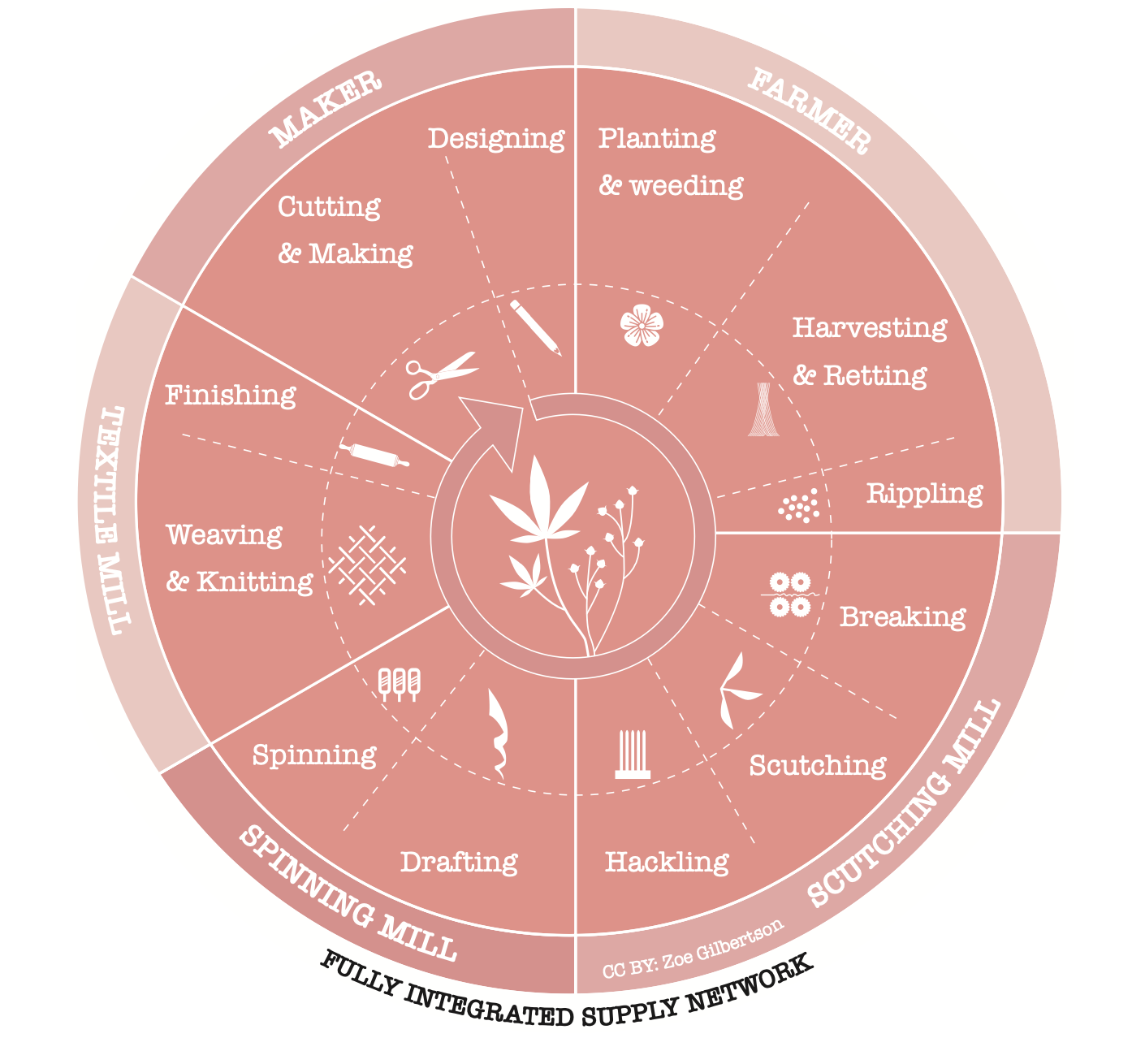
The upshot of Gilbertson's rigorous research is a remarkably detailed, action-oriented report, "Bioregional Resilience through Bast Fibres: Exploring Machinery and Methods to Support UK Fibre Production," published in June 2024.
The report found that “clothing has the potential to make connections to land and people past and present, once the stories bound up in the creation of cloth come alive. The true values of production will be found in collaboration, local pride, ecological resilience and fair farming practices…..Starting from scratch, we have an opportunity to develop resilient, small-scale flexible systems that cope with the variable nature of the weather and work with seasons, nature, climate and people and not profit extraction."
It turns out that growing crops of flax and hemp on a bioregional basis in the UK is quite attractive as an agricultural, economic, and cultural proposition. Gilbertson concluded that fiber-growing "could support a wide range of material outputs, skills, livelihoods across the UK with many knock-on benefits for farming and society, reducing reliance on fossil-fuel materials." She continued:
There is increasing demand for natural materials to replace energy-intensive, fossil-fuel-derived polluting materials. Food and building materials derived from hemp and flax are simpler to produce than textiles. A new system could begin with these to generate revenue for farmers, alongside developing collective skill in processing textile yarn. We could ask the purpose of making more textiles, considering if it’s necessary when the world is awash with so much clothing. Textile fibre from flax and hemp could support other more useful products, such as food and building materials, which provide an excellent break crop in rotation, create monetary value, and connect people through culture.
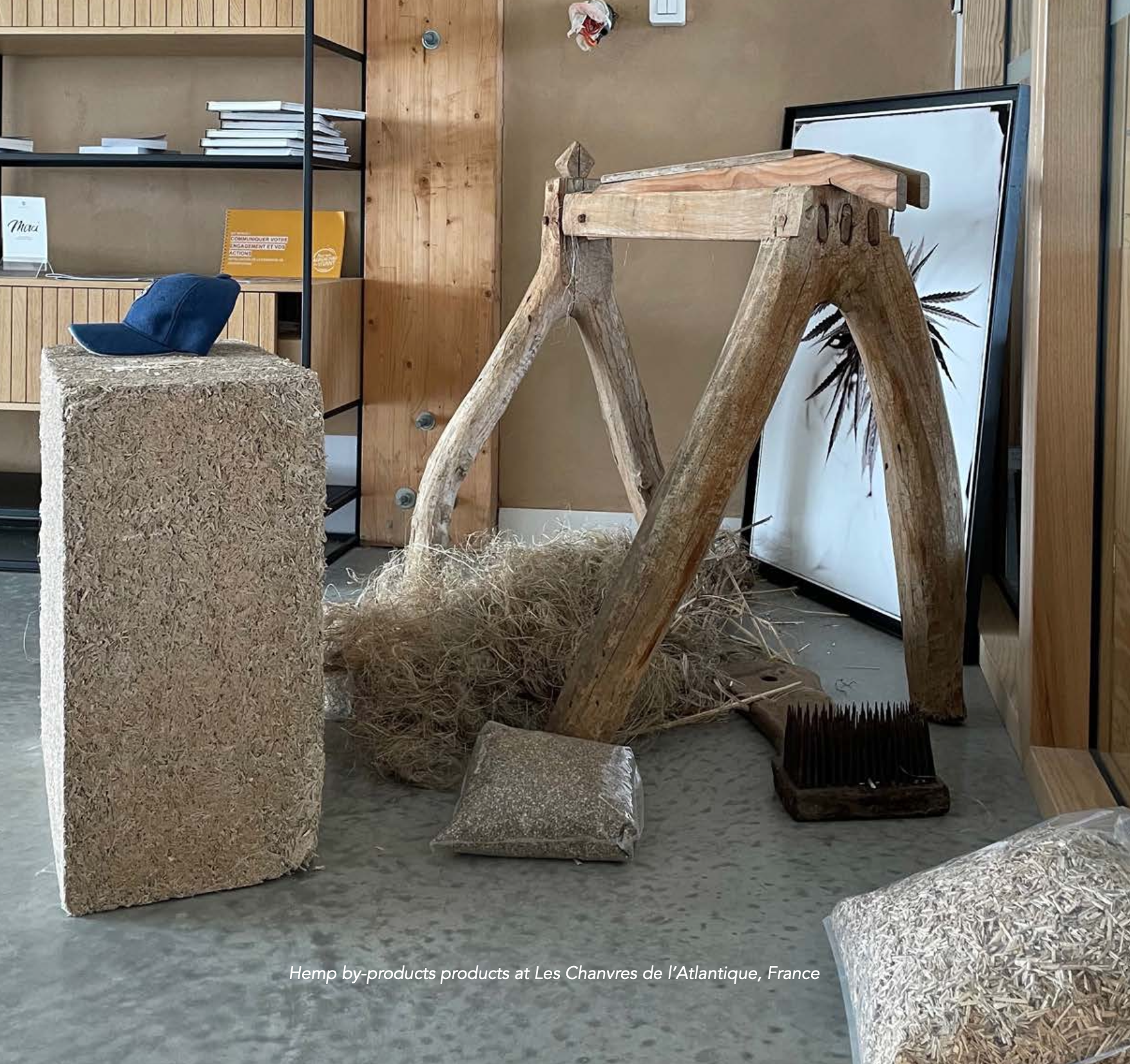
To achieve this ambitious vision of bioregional fibersheds, however, a lot of work must be done. Investment in small-scale, open-source machinery to process the fibers is essential, for example. Locally minded collectives and community groups must be formed to manage the equipment and coordinate the system. New types of supply chains to connect farms with rural communities and cities must be created.
What's impressive is how many artisanal fiber growers, local clothing producers, and entrepreneurial small garment businesses already exist. Gilbertson's travels brought her into contact with "seed to closet" initiatives, traditional clothing crafts, clothes swaps, mending and upcycling projects, craft workshops, campaign groups, and much else.
The near-term challenge, she concluded, is to bring the diverse players together, so that they can begin to collectively imagine, design, and build new types of relationships and bioregional infrastructures.
To help goose this process along, Gilbertson recently founded a not-for-profit company called Liflad CIC [community interest company], with a Substack collection of essays, and the Bast Fibre Network to support development of an agriculturally centered fashion and textile system. Gilbertson is also actively engaged in developing a bioregional textile industry in South West England, and collaborating with the fashion collective Fashion Act Now.
Gilbertson new website, Bast Fibre Commons, hopes to facilitate the cross-fertilization of ideas and support among fashion innovators. The site includes a map of bast fibre initiatives, a repository of research resources, and community-based development programs.
Another initiative for weaving together far-flung, like-minded fashion innovators is a website called OurCommon.Market, created by Fashion Act Now. The site "is not a marketplace as such, but a sort of gathering and connection space," said Gilbertson. "It's a space for highlighting diverse community-centered clothing and textile products."
OurCommon.Market aims to convene an international network of fashion innovators by offering multiple resources: a journal of news and commentaries, an events bulletin board, a space for co-learning, a map for finding clubs, makerspaces, and workshops near you, and much else. Here's how the website describes its goals:
"Community-driven clothing cultures offer an alternative to the dominant fashion system, emphasising sufficiency and wellbeing and reconnecting people with traditions and culture. These communities practice visible mending, craft revitalisation, and regenerative fibre production. However, these alternatives have often been fragmented, erased, eroded, and ignored. We propose to address this by building a translocal digital commons to unearth, explore, connect, and support diverse clothing communities demonstrating regenerative practices. Our goal is to contribute to the visibility and viability of alternate systems and encourage participation in them."
You can listen to my podcast interview with Zoe Gilbertson here.
Recent comments